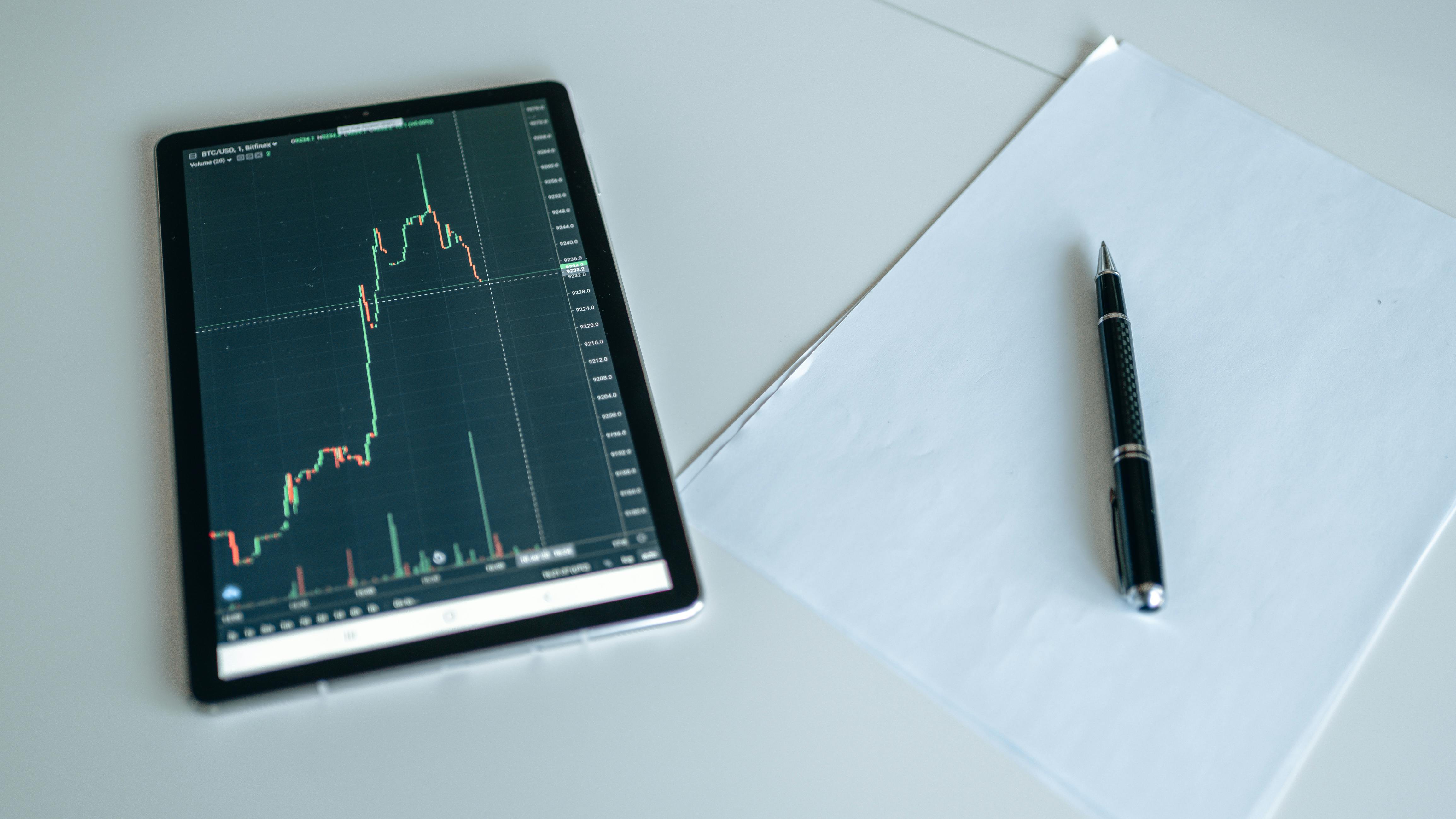
A project best practice implementation case study!
MANUFACTURING: A BEST PRACTICE IMPLEMENTATION CASE STUDY
The assignment
Sharpline Automation SA. limited. (SAPL) had a mix of new and ongoing projects with durations ranging from 3 to 8 months. The company took up the renovation of CNC machines as its core business, as well as designing and delivering new machines based on customer requirements.
The challenge
They had the necessary resources to run the 22 or so projects, but on the condition that they perform optimally. There were 2 General Managers, one from the Mechanical side and the other from the Electrical and Electronics discipline, all of whom came into play depending on the type of job. The problem was to optimize the available resources so that the projects could be carried out on time.
The facilitator/consultant was tasked with putting together a system to track each project to enable proper reporting (feedback) and facilitate timely action to avoid delays and resultant delays.
A hybrid Lean & Project Management model was implemented that took the best of both and delivered a practical, easy-to-use method for project control.
Objectives
The Facilitator/Consultant was entrusted with the task of training and guiding the team to achieve the following objectives:
• Learn best practices that can deliver high and predictable performance
• Guide the team to implement them in the projects in question.
• Let them act on their own for a couple of 2-week periods with check-ins after each
• Review implementation regularly to get feedback, learn lessons, remove barriers, and ensure success
2 day workshop and planning
The exercise began with a 2-day workshop attended by the project team, including general managers, planning engineers, project coordinators, mechanical, electrical, electronic, software and hardware engineers, and product distribution manager. procurement and labor.
The workshop was 50:50, Learning: Practice sessions with the teams, divided into groups of 3 to 4, doing exercises on about 4 selected ongoing projects.
As part of the workshop, building on the project’s Master Plan and Monthly Plans, they were shown how to microplan and prepare the 2-week plan as a subset of the monthly plan.
Execution and Monitoring and Control
Since everyone was running projects, it was a learning on the job of best practices. The project was executed and monitored and controlled using the 2-week iterative cycle. Emphasis was placed on removing restrictions and resolving issues each week to keep a close eye on likely impediments.
daily action
Daily activities were listed from the weekly plan at the start of the day (the advantage of doing this was also demonstrated at the end of the previous day), and the work was done and monitored at the end of the day. Activities not completed and the reasons why they were not completed and lessons learned were recorded. Corrected or revised activities were included in the next day’s list.
In this way, daily activities were monitored throughout the week and continued for the following week, at which point a new cycle began.
Full-day review sessions were held 2 weeks after the workshop and a second review 2 weeks after the first review.
These reviews claimed to help them establish a collaborative framework that is a Lean highlight and also to get used to the daily monitoring regimen.
Implementation Highlights
Many practical concepts and enabling tools that the teams learned and implemented at the Workshop and also during the course of the review sessions were:
• 7 waste in projects and how to increase efficiency by controlling activities that do not add value
• 5S analysis for workplace management
• Importance of a Work Breakdown Structure (WBS) for each project
• Risk management and project limitations
• Collaborative planning and daily Huddle/Stand-up meetings
• Continuous improvement and PDCA
• Planned Percentage Complete (PPC) charts and histograms of reasons for failure, developed after one week of activity, providing useful information for rapid corrective/preventive actions for coordinators and project management.
Results/Observations
o Best practices learned: planning daily activities in numbers, recording reasons for non-compliance, micro-planning activities, weekly planning, problem record keeping to track and overcome impediments
o Benefits gained from this engagement: team members took ownership of their work due to collaborative culture, gained more knowledge about activities due to collaborative planning approach, daily planning documentation was a big new change, reasons of delay were quickly identified, Stress levels were reduced as the work was distributed to everyone, all the way down to the “Doer”, tracking and keeping on schedule became easier
o Areas of improvement for future projects: Improvement in attitude and participation in work, Better planning, monitoring and control of projects, Improved visibility into work progress
o Senior management could focus on other vital areas of the business such as business development. The weekly review of the data generated from the daily activities indicates the corrective/preventive action required for each project.
o Project coordinators could pay more attention to preparing weekly plans for the coming week than to frequent shootouts.